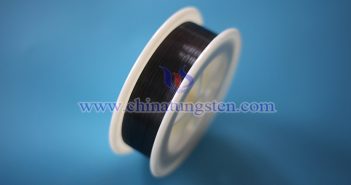
As a special metal material with high hardness and a high melting point, cut-resistant tungsten wire is widely used in precision machining, semiconductor manufacturing, medical equipment, and other fields. Its maintenance requires consideration of both material properties and working conditions. Below is a systematic care guide addressing storage environment, usage procedures, regular inspection, cleaning processes, transportation protection, and recycling management: I. Storage Environment Control for Cut-Resistant Tungsten Wire Temperature and Humidity Requirements Store at room temperature (15–30°C) with relative humidity…