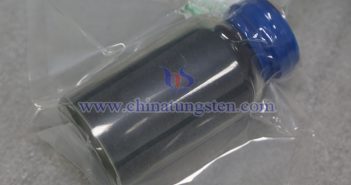
Tungsten disulfide (WS?), a transition metal sulfide, typically appears as a gray-black powder. It exhibits excellent lubricating properties with a low friction coefficient and maintains stability under extreme conditions such as high temperature and pressure, making it commonly used as a solid lubricant. Additionally, it shows promising application potential in fields such as catalysis, energy storage, and semiconductors, positioning it as a highly regarded multifunctional inorganic material. Several preparation methods exist for tungsten disulfide, with the following being some of…